What are the Types of Production System?
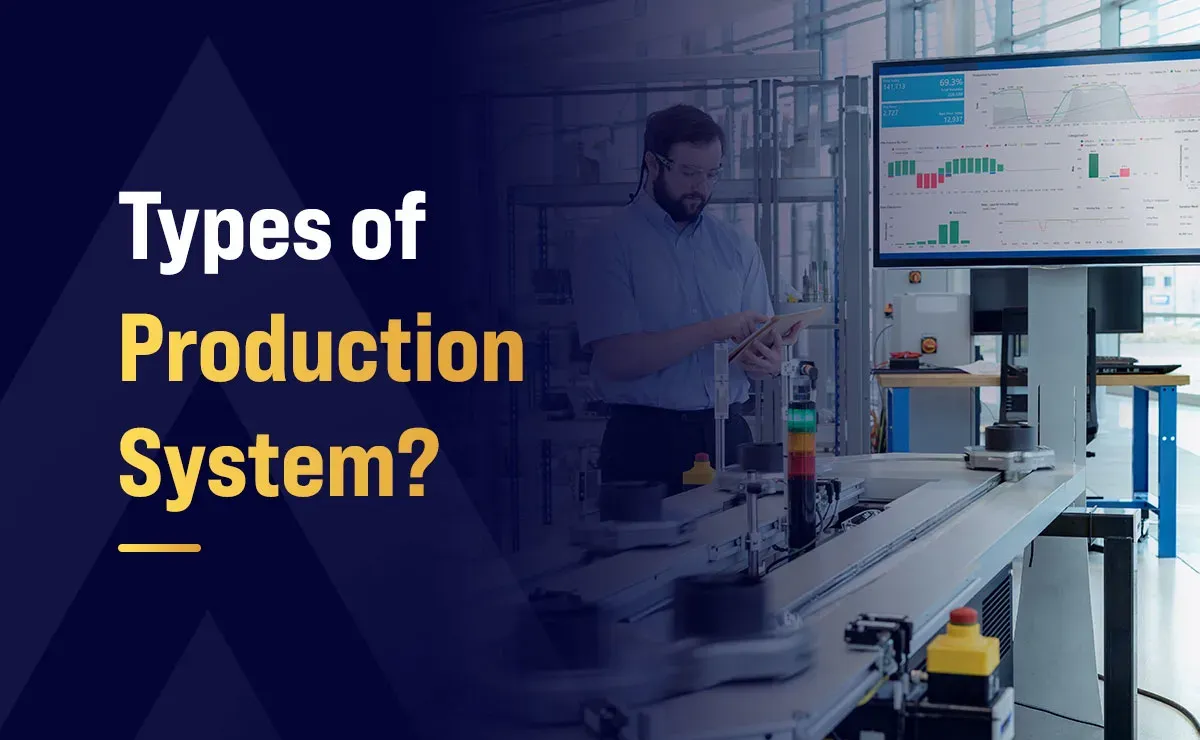
Manufacturing serves as the foundation of all industries, guaranteeing that products are readily available to satisfy consumer needs. The efficiency and effectiveness of a company’s production strategy determine its market success. Production systems define how goods are manufactured, impacting efficiency, cost, and scalability.
Different industries adopt different production approaches based on factors like product variety, volume, cost-effectiveness, and flexibility. Selecting the optimal production system is essential for businesses to achieve peak efficiency while keeping pace with market requirements.
This article explores the different types of production systems, their characteristics, advantages, disadvantages, and industry examples.
What is a Production System?
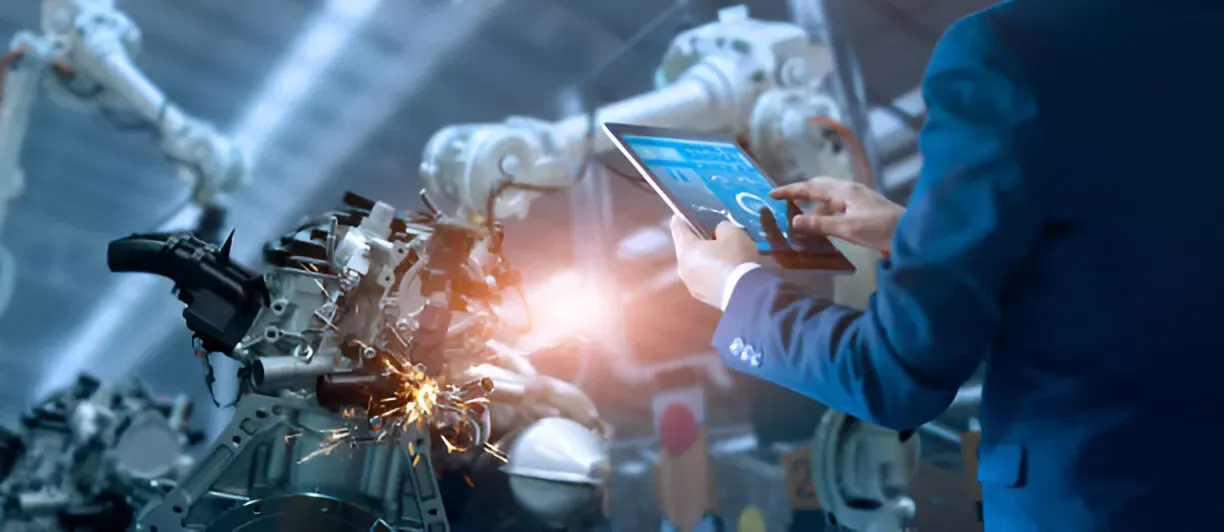
A production system is a structured process that transforms raw materials (input) into finished products (output) through various manufacturing operations. It acts as the backbone of manufacturing, ensuring that resources are efficiently utilized to produce goods and services that meet market demands.
At its core, a production system can be visualized as a black box where inputs (such as raw materials, labor, energy, and information) enter, undergo various processes, and emerge as finished products. The transformation of input to output can take place through different methods, including:
- Separating: Splitting one material into multiple parts (e.g., cutting a wooden plank).
- Putting Together: Combining different materials to create a single product (e.g., assembling furniture).
- Detaching: Shaping materials while producing waste (e.g., carving wood with a lathe).
- Forming: Reshaping materials without waste (e.g., hammering metal into shape).
- Quality Adaptation: Enhancing product properties (e.g., surface treatment of metals).
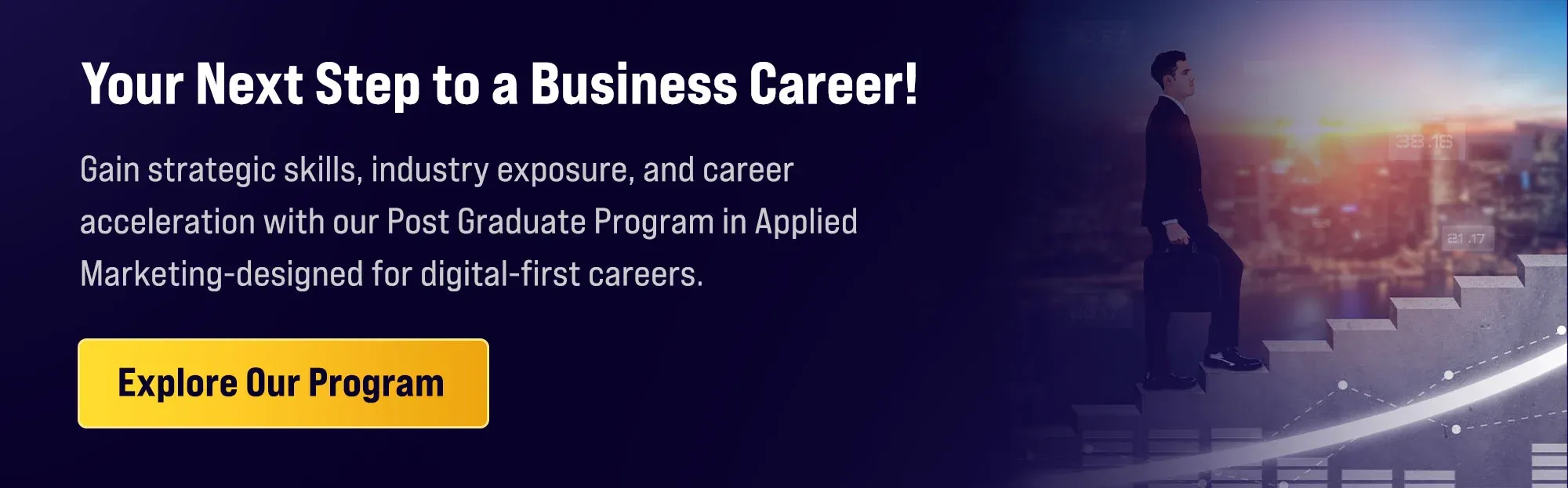
Types of Production System
Different industries adopt various types of production systems in operation management based on factors like product demand, customization requirements, cost considerations, and technological capabilities. The following outlines the main categories of production systems, each with unique features, benefits, and limitations.
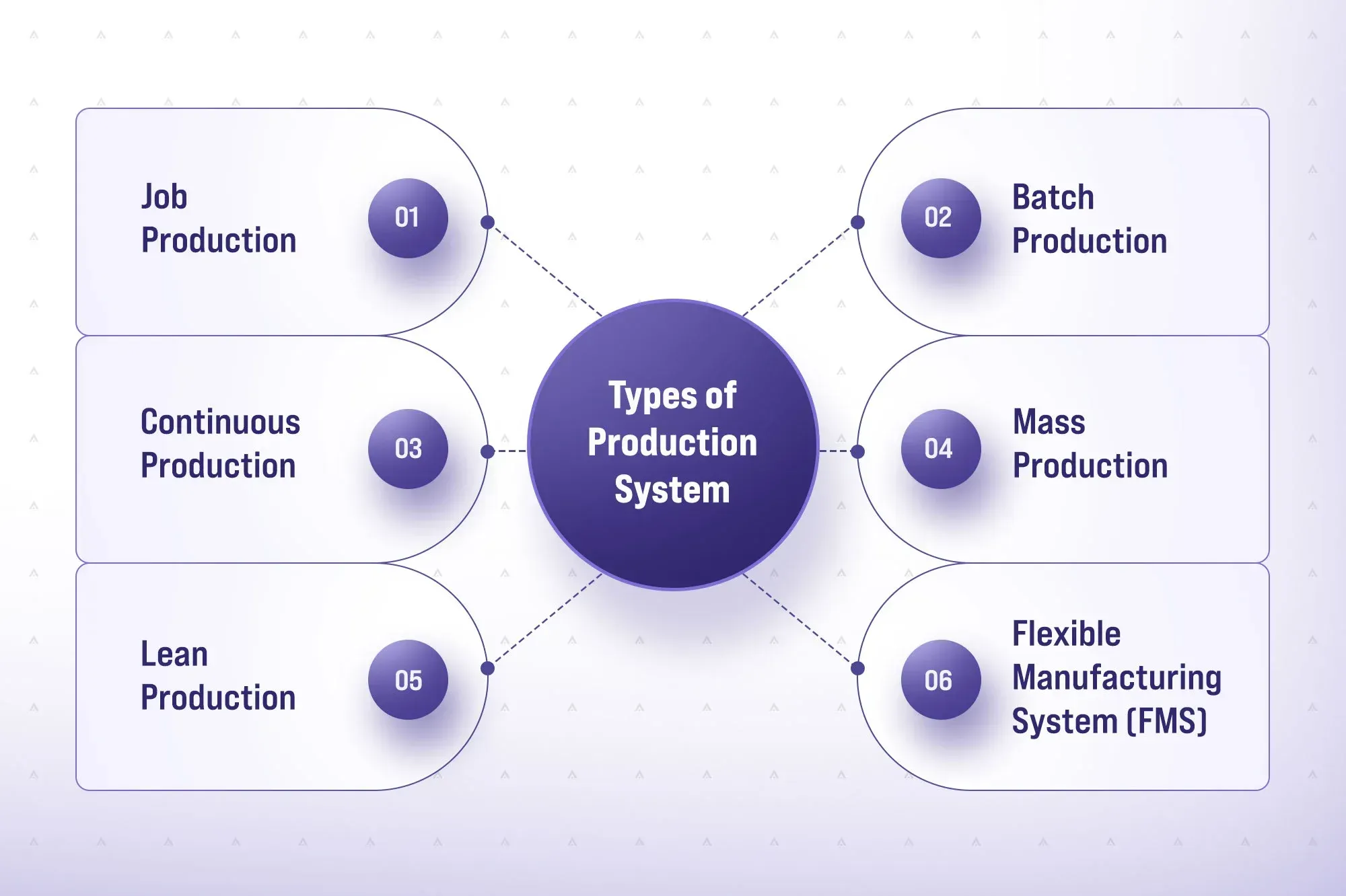
Job Production
Job production focuses on manufacturing products individually or in small quantities, often tailored to customer specifications. This system is best suited for customized, high-quality products that require specialized skills and craftsmanship.
Characteristics
- Each product is unique and customized according to specific requirements.
- Production is labor-intensive, requiring skilled workers with expertise in their craft.
- The process is usually slow, as each item undergoes separate stages of production.
- Machinery and tools are flexible, allowing for diverse production tasks.
- High variability in work schedules due to different product specifications.
Advantages
- It enables extensive product personalization to cater to specific customer preferences.
- It guarantees exceptional quality through meticulous attention to detail during manufacturing.
- Workers gain specialized skills, leading to high craftsmanship and expertise.
- It is well-suited for crafting intricate and sophisticated designs beyond the scope of mass production.
Disadvantages
- The production process is time-consuming, leading to longer lead times.
- It incurs higher production costs due to manual labor and customization requirements.
- It is subject to low efficiency as machines and workers frequently switch tasks.
Examples
- Custom furniture making
- Tailor-made suits
- Handmade jewelry
- Prototype development in the automotive industry
Batch Production
Batch production involves manufacturing a set quantity of identical products before switching to another batch. It strikes a balance between tailored customization and operational efficiency, perfect for medium-scale output.
Characteristics
- Production is carried out in batches, with each batch undergoing a complete manufacturing process before starting the next.
- Machines and tools require reconfiguration between batches to accommodate different products.
- A moderate level of customization is possible while maintaining efficiency.
- More standardized than job production but still allows some variation.
- Requires strategic scheduling to reduce idle time and enhance resource efficiency.
Advantages
- It lowers per-unit production expenses compared to job production by leveraging bulk manufacturing advantages.
- It allows moderate flexibility in product design and variations.
- It optimizes workforce and machinery usage, improving overall productivity.
- It ensures consistent quality within each batch.
Disadvantages
- Setup time between batches can lead to production delays.
- It requires storage space for work-in-progress inventory.
- It is less flexible than job production when it comes to fully customized products.
Examples
- Baked goods (pastries, loaves, biscuits)
- Medications and healthcare tablets
- Apparel and fabric materials
- Published periodicals and literature
Mass Production
Mass production involves the high-volume creation of uniform goods using fully automated systems. It focuses on efficiency, cost reduction, and consistency.
Characteristics
- Production is continuous, with products moving through an assembly line.
- Minimal customization, as products are standardized.
- Specialized machinery and workers are used to enhance productivity.
- Bulk manufacturing reduces individual unit costs through scaled operations.
- Standardized quality checks maintain product uniformity throughout the process.
Advantages
- It delivers unmatched efficiency, producing vast quantities at minimal expense.
- It ensures uniformity and consistent product quality.
- It requires minimal labor due to automation, reducing human errors.
- Due to a faster production rate, it helps meet high market demand.
Disadvantages
- It incurs a high initial investment in machinery and infrastructure.
- It has limited flexibility, making it difficult to alter product designs.
- As employees may perform repetitive tasks, it can lead to job dissatisfaction.
Examples
- Automobile manufacturing (e.g., Toyota, Ford)
- Smartphone production (e.g., Apple, Samsung)
- Home appliances (e.g., washing machines, refrigerators)
- Fast-food chains (e.g., McDonald's, Burger King)
Continuous Production
Continuous production operates 24/7 with minimal interruptions, often used in industries where products must be manufactured in a continuous flow.
Characteristics
- Production runs without breaks, ensuring an uninterrupted supply.
- Heavily automated systems require minimal human intervention.
- Highly specialized machinery is used to maintain efficiency.
- Built for ultra-high output capacities without compromise.
- Rigorous quality protocols ensure every product meets exact specifications.
Advantages
- It maximizes efficiency with minimal downtime.
- It helps reduce labor costs due to automation.
- It can produce consistent and uniform products at scale.
- It is ideal for industries requiring a steady supply chain of goods.
Disadvantages
- It requires a significant capital investment in infrastructure and technology.
- It has limited flexibility, as switching between products is complex.
- It needs continuous maintenance and monitoring to prevent breakdowns.
Examples
- Oil refineries
- Power plants
- Steel and cement manufacturing
- Chemical production (e.g., fertilizers, paints)
Lean Production
Lean production focuses on minimizing waste and maximizing efficiency while maintaining high-quality standards. It aims to eliminate non-value-adding processes.
Characteristics
- Emphasizes waste reduction to improve resource efficiency.
- Uses just-in-time (JIT) inventory management to reduce excess stock.
- Ongoing refinement (Kaizen) lies at the heart of this methodology.
- Promotes teamwork across departments to foster innovation.
- Focuses on delivering value to customers.
Advantages
- It helps reduce operational costs by eliminating unnecessary steps.
- It improves overall productivity and efficiency.
- It helps enhance product quality through continuous improvement strategies.
- It also empowers employees to contribute actively to troubleshooting.
Disadvantages
- It requires constant monitoring and process adjustments.
- Heavy dependence on supplier efficiency for JIT inventory.
- The implementation process may pose difficulties in certain sectors.
Examples
- Toyota Production System
- Consumer electronics assembly
- Made-to-order PCs (e.g., Dell configurations)
6. Flexible Manufacturing System (FMS)
A Flexible Manufacturing System (FMS) combines automation, robotics, and computerized controls to produce diverse products with rapid adaptability.
Characteristics
- Utilizes CNC machines for ultra-precise fabrication.
- Seamlessly transitions between varying product lines.
- Minimizes delays during production changeovers.
- High efficiency while still allowing for some customization.
Advantages
- It is highly flexible in adapting to different product requirements.
- It reduces inventory costs due to efficient production planning.
- It maximizes the use of automated technology, increasing efficiency.
Disadvantages
- It does not require a significant initial investment in technology and equipment.
- It needs a skilled workforce to manage automated systems.
- The maintenance and troubleshooting process involved in this system can be complex.
Examples
- Aerospace industry (e.g., Boeing, Airbus)
- Car manufacturing (e.g., Tesla’s automated production lines)
- High-tech industries (e.g., semiconductor manufacturing)
FAQs
Q1. What are the three types of production system?
Ans: The three main types of production system are:
- Job Production – Involves creating one-off or highly customized products tailored to individual customer requirements. Example: Custom furniture making.
- Batch Production – Produces goods in specific quantities or batches before switching to a different product. Example: Bakery products.
- Mass Production – Centers on high-output, standardized item fabrication via automation. Example: Automobile production.
Q2. What are the four production processes?
Ans: The four key production processes are:
- Separating – A process where a single input is split into two or more outputs. Example: Cutting wood into multiple planks.
- Putting Together (Assembly) – Combining different components to form a final product. Example: Assembling parts of a car.
- Forming – Reshaping materials without subtractive processes. Example: Metal shaping in manufacturing.
- Quality Adaptation – Modifying an item’s properties to enhance durability, appearance, or function. Example: Applying paint or coating to a metal surface.
Conclusion
Production systems play a vital role in shaping the efficiency, cost-effectiveness, and scalability of manufacturing across industries. From job production, which focuses on customization, to mass and continuous production, which emphasizes efficiency and high output, each system is designed to meet specific business needs. Additionally, lean and flexible manufacturing systems bring innovation by optimizing resources and adapting to market changes.
With the rise of AI-driven production systems, industries are embracing intelligent automation to enhance decision-making and streamline operations. Understanding these production systems allows businesses to select the most suitable approach, ensuring maximum productivity and competitiveness in a rapidly evolving marketplace.