Types of Production Management
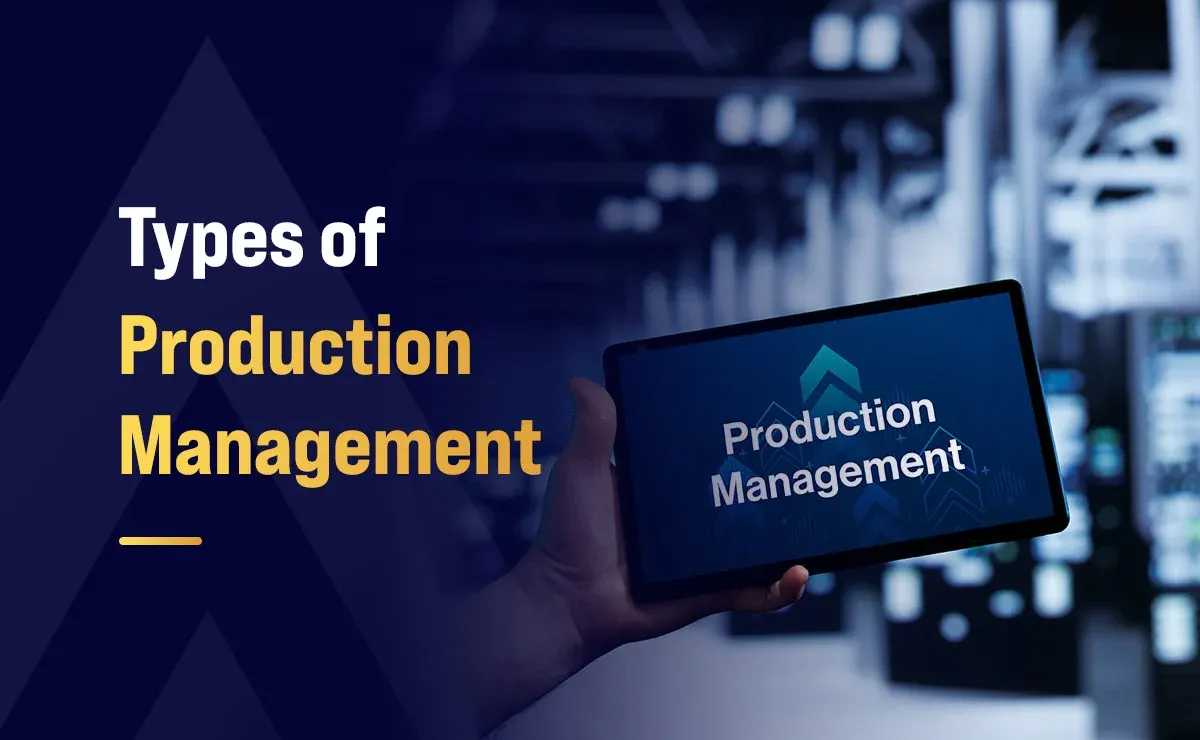
Production management is essential for converting raw materials into final goods with optimal efficiency. It involves the strategic management, execution, and supervision of production processes to ensure quality, cost-effectiveness, and timely delivery. While "operations management" is often used interchangeably with "production management," the latter focuses specifically on manufacturing activities.
To optimize production, businesses adopt different types of production management based on the nature of the product, market demand, and resource availability. This article delves into different production management approaches, highlighting their importance, key features, and practical uses.
What are the Various Forms of Production Management?
Process Manufacturing Method
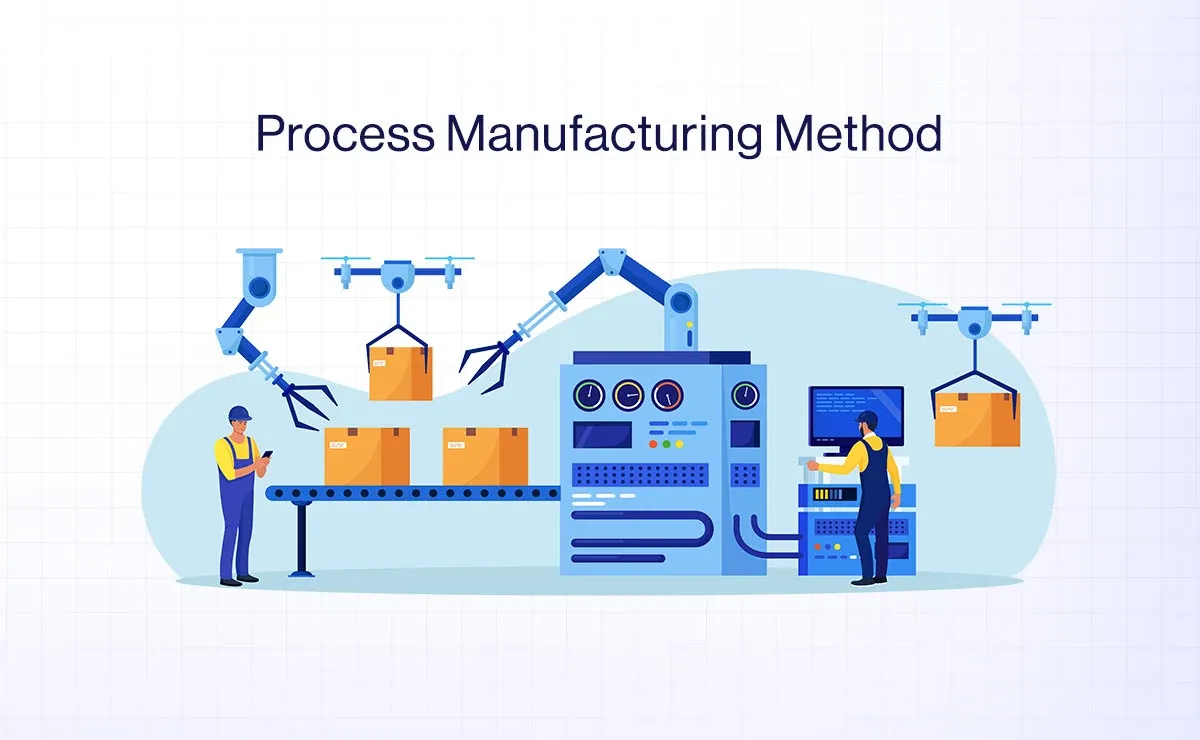
Process manufacturing is a highly structured production method where raw materials undergo a series of chemical, mechanical, or biological transformations to create a final product. Unlike discrete manufacturing, where individual components can be assembled and disassembled, process manufacturing results in goods that cannot be broken down into their original ingredients once the transformation is complete.
This method is commonly used in industries that require precise formulations, consistency, and large-scale production. It can be executed as either continuous production, where manufacturing runs non-stop, or batch production, where materials are processed in fixed quantities.
Key Characteristics
- Can operate as a continuous or batch-based production system.
- Generally, it utilizes advanced machinery and precisely controlled conditions.
- Best suited for industries that demand high consistency and quality.
Common Applications
- Pharmaceuticals: Used for manufacturing medicines, vaccines, and other medical formulations.
- Food & Beverage: Applied in the production of soft drinks, dairy products, packaged foods, and canned goods.
- Chemicals & Plastics: Essential for producing fertilizers, detergents, synthetic materials, and industrial chemicals.
Schedule Management
Schedule management focuses on planning, coordinating, and optimizing the manufacturing timeline to ensure smooth and efficient operations. It involves setting realistic deadlines, allocating resources effectively, and making necessary adjustments to accommodate unforeseen challenges such as equipment failures, supply chain management disruptions, or labor shortages.
Adopting an organized scheduling strategy helps companies reduce idle time, boost output, and fulfill orders promptly. Effective schedule management not only improves workflow efficiency but also helps in cost reduction by avoiding delays, overproduction, and resource wastage.
Key Characteristics
- Streamlines workflow to enhance efficiency and minimize production delays.
- Requires seamless coordination between teams, machinery, and material supplies.
- Optimizes resource utilization, reducing overall production costs.
Common Applications
- Automobile Manufacturing: Ensures synchronized assembly of vehicle components.
- Construction Projects: Manages material deliveries and workforce scheduling for timely project completion.
- Retail & E-commerce: Regulates inventory levels and restocking cycles to meet consumer demand.
Flow Management
Flow management is a strategic approach to directing and optimizing the movement of materials, components, work-in-progress items, and finished goods throughout the production and distribution process. It ensures that all operations involved in manufacturing or delivering a product are well-coordinated, minimizing inefficiencies and enhancing overall productivity.
In a manufacturing facility, flow refers to the sequential steps that products undergo during fabrication. When all products follow the same production steps, they move through a single unified flow. However, when different products require unique processing steps, multiple production flows exist. These flows, also called value streams, determine how efficiently raw materials transform into finished goods and reach the consumer.
Key Characteristics
- Ensures a continuous movement of work-in-progress inventory for efficient production.
- Incorporates automation and lean manufacturing to enhance productivity.
- Minimizes storage needs and reduces idle time between production stages.
Common Applications
- Textile Industry: Oversees seamless transitions from fabric weaving to dyeing and stitching.
- Electronics Manufacturing: Ensures seamless operations in assembling circuit boards and integrating parts.
- Food Processing: Facilitates efficient movement through sorting, cutting, packaging, and distribution.
Batch Production
Batch production is a manufacturing process in which a specific quantity of identical products is produced simultaneously before moving on to the next batch. Unlike continuous production, where items are made in an ongoing process, batch production allows manufacturers to control the size, frequency, and specifications of each batch based on demand, customer preferences, or production requirements.
Each batch follows a structured sequence of production stages, and a new batch cannot begin a specific phase until the previous one has completed it. This ensures a systematic workflow while allowing for adjustments and quality control between batches.
Key Characteristics
- Manufacturing is carried out in predetermined batch sizes.
- Equipment and machinery can be adjusted to accommodate different products.
- Ideal for industries with variable demand and product customization needs.
Common Applications
- Bakeries: Creating various cake flavors in controlled production batches.
- Textile Manufacturing: Dyeing fabrics in multiple colors as per requirements.
- Pharmaceuticals: Producing medicines in specific quantities based on market demand.
Job Production
Job production is a manufacturing method where products are created individually based on specific customer requirements. Each order is unique, and production only begins once an order is placed. This approach is commonly used in custom-built homes, artwork, aerospace manufacturing, and tailored services.
It requires skilled professionals or specialized teams, making it time-intensive but highly rewarding. While job production offers high-quality, personalized outputs, it also demands greater effort, resources, and time compared to mass production. Businesses often charge premium prices for these bespoke, tailor-made solutions.
Key Characteristics
- Products are uniquely designed and customized to meet specific client needs.
- Skilled craftsmanship and specialized tools are essential for production.
- Each project is distinct, with no direct repetition from previous work.
Common Applications
- Luxury Jewelry: Designing and crafting bespoke pieces tailored to customer preferences.
- Construction Industry: Developing custom-built homes, bridges, or ships based on unique specifications.
- Printing Press: Creating personalized books, invitations, and artistic prints with custom layouts.
Continuous Production
Continuous production is a highly automated manufacturing process that operates non-stop, producing large volumes of identical or similar goods. This approach works best for sectors demanding precision and uniformity, like food manufacturing, drug production, and chemical processing.
Operations continue non-stop with little manual input, guaranteeing smooth processes and uniform product management standards. As it doesn’t accommodate product variations, continuous production is best suited for bulk manufacturing with steady demand. Its automated nature and high productivity make it economical for mass manufacturing.
Key Characteristics
- Runs continuously with minimal interruptions, maximizing efficiency.
- Requires substantial investment in automated systems and advanced infrastructure.
- Ideal for industries with steady, high-volume demand for standardized products.
Common Applications
- Petrochemical Industry: Refining crude oil into gasoline, lubricants, and other byproducts.
- Cement Production: Operating non-stop to produce bulk quantities for large-scale construction.
- Steel Industry: Processing raw materials into steel sheets, bars, and other structural components.
Batch Flow
Batch flow is a system where goods are made in predefined groups instead of non-stop or individually. Each batch moves through each stage of production together, meaning a new batch cannot start a stage until the previous one is complete.
This method allows customization between batches, such as changes in size, color, or design, making it ideal for small to medium-sized manufacturers. It also enables quality checks at each stage, ensuring high product standards and efficient machine utilization.
Key Characteristics
- Offers a middle ground between adaptability and operational effectiveness.
- Allows for customization while maintaining large-scale production capabilities.
- Enables continuous movement of batches through different stages without delays.
Common Applications
- Pharmaceuticals: Manufacturing various drug formulations in regulated batch cycles.
- Consumer Goods: Producing household essentials like detergents and personal care items.
- Medical Equipment: Manufacturing products such as syringes, test kits, and surgical instruments.
Process Flow
Process flow refers to the structured sequence of steps a product follows from its initial concept to final delivery. It encompasses idea generation, development, production, marketing, sales, and after-sales service. Each stage is interconnected, meaning disruptions in one phase can impact the entire system.
Streamlining process flow management leads to uninterrupted workflows, better resource allocation, and on-time shipments. By evaluating and fine-tuning each phase, firms can increase productivity, cut downtime, and boost client contentment.
Key Characteristics
- Adheres to a fixed sequence of operations for uniform production.
- Ensures uniformity in product quality for every item.
- Utilizes automated systems to increase output while reducing human involvement.
Common Applications
- Paper Industry: Converting raw pulp into finished paper products through continuous processing.
- Sugar Refineries: Refining sugarcane into granulated sugar using a systematic flow.
- Automobile Manufacturing: Assembling vehicle components in a structured, step-by-step process.
Job Shop
Job shop manufacturing is a versatile production method designed for small-scale, custom-made orders. It is ideal for businesses that produce unique, made-to-order (MTO) products in small batches, ensuring high flexibility. Unlike mass production, job shops utilize general-purpose machines to handle a variety of tasks and workflows.
The process prioritizes job scheduling, specialized routing, and just-in-time (JIT) workflows to enhance efficiency, reduce waste, and meet customer-specific requirements with precision and adaptability.
Key Characteristics
- Perfect for crafting diverse, tailor-made items in limited volumes.
- Workstations are organized based on specific functions rather than a linear process.
- Requires highly skilled labor to adapt to varying project management requirements.
Common Applications
- Automobile Repair Centers: Servicing and repairing different vehicle models with unique issues.
- Metal Fabrication Workshops: Crafting custom metal components and specialized tools.
- Prototype Development Labs: Creating unique product designs for testing and refinement.
Assembly Line
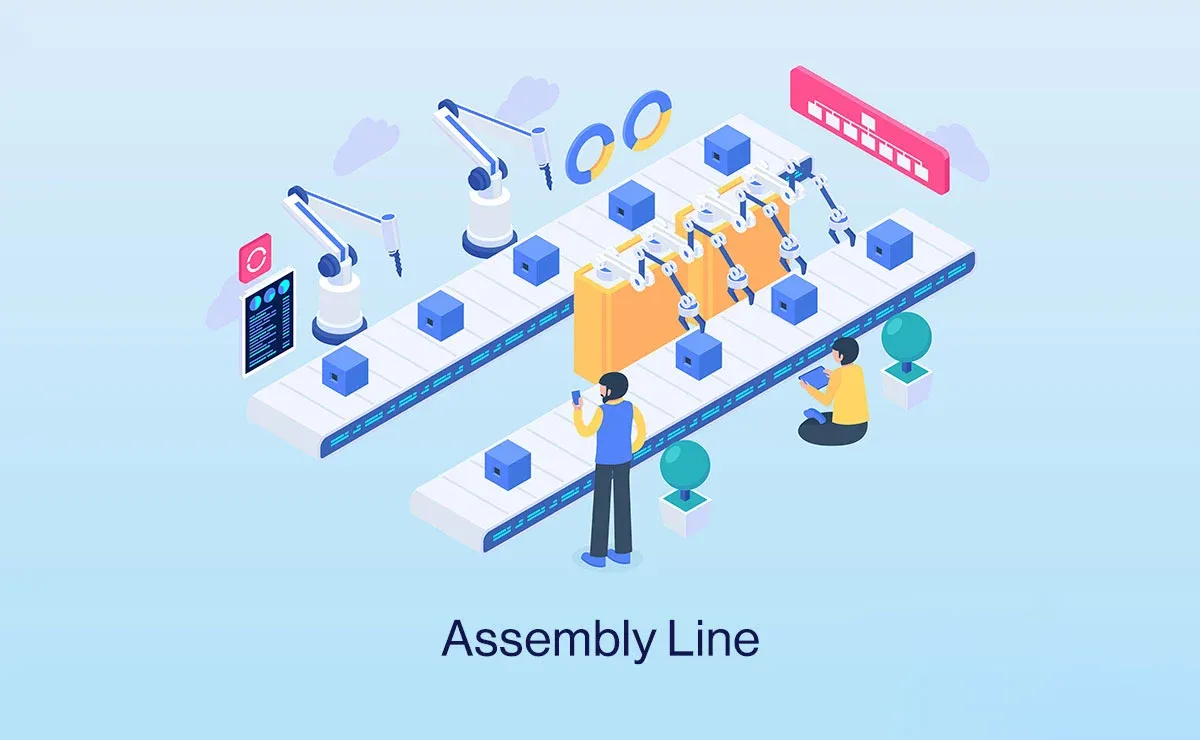
An assembly line is a manufacturing system where a product is built through a step-by-step sequence, with each worker or machine handling a specific task. This technique is common in high-volume manufacturing, promoting productivity and lower expenses. Instead of relying on skilled artisans to craft entire products, workers are trained for specialized roles, such as attaching a component or tightening a bolt.
This structured workflow enhances productivity, minimizes errors, and accelerates production speed, making it a fundamental approach in industries like automobile, electronics, and furniture manufacturing.
Key Characteristics
- Goods progress through a fixed pathway, with dedicated workstations handling distinct functions.
- Workers or machines handle repetitive, specialized functions, improving efficiency.
- Streamlined processes enable mass production with minimal delays.
Common Applications
- Electronics Manufacturing: Assembling consumer electronics like televisions, refrigerators, and smartphones.
- Automobile Production: Streamlining the mass production of cars with standardized components.
FAQs
Q1. What are the three types of production planning?
Ans: Production planning is categorized into:
- Job Production Planning: Focuses on individual, customized product manufacturing.
- Batch Production Planning: Produces goods in fixed quantities to balance demand and efficiency.
- Mass Production Planning: Ensures high-volume, continuous production to meet market needs.
Q2. What are the types of production systems in operations management?
Ans: Production systems in operations management include:
- Intermittent Production: Involves job shop and batch production, where production is not continuous.
- Continuous Production: Includes mass production and process manufacturing, ensuring uninterrupted production flow.
Conclusion
Effective production management is crucial for businesses aiming to enhance efficiency, maintain quality, and meet customer demands. Different production management methods—such as process manufacturing, batch production, job production, and continuous production—offer unique advantages based on industry needs and product requirements.
Choosing the appropriate strategy allows businesses to maximize assets, simplify processes, and increase earnings. Whether it’s large-scale mass production or highly customized manufacturing, understanding these production strategies ensures businesses remain competitive and adaptable in a dynamic market.