What is the Scope of Operations Management?
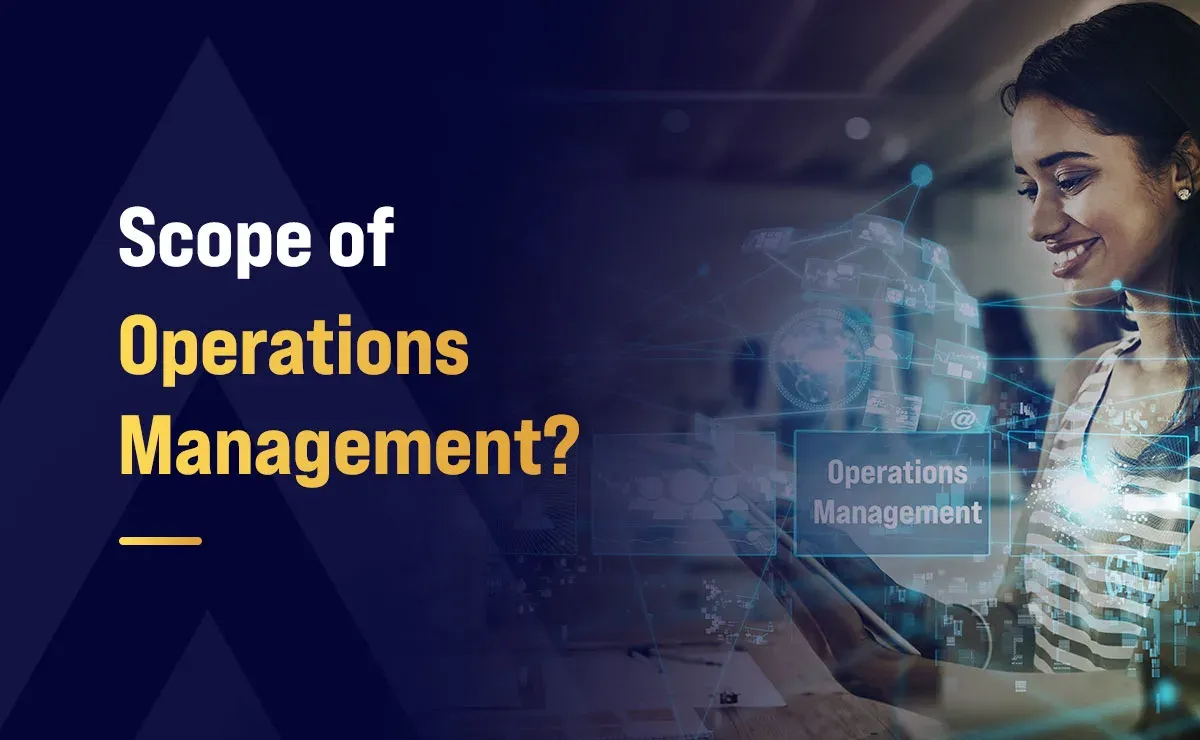
Operations management (OM) is one of the most crucial functions in any business, regardless of its size, industry, or nature. From factories to service providers, OM is essential in guaranteeing that products and services are created effectively to satisfy consumer demands.
The scope of OM is vast, covering strategic planning, resource management, quality control, supply chain coordination, and customer satisfaction. By balancing efficiency, cost-effectiveness, and innovation, operations management drives organizational success in today’s competitive business environment.
This article explores the key areas that define the scope of OM, providing practical insights to help you understand its critical role in real-world business operations.
Objectives of Operations Management
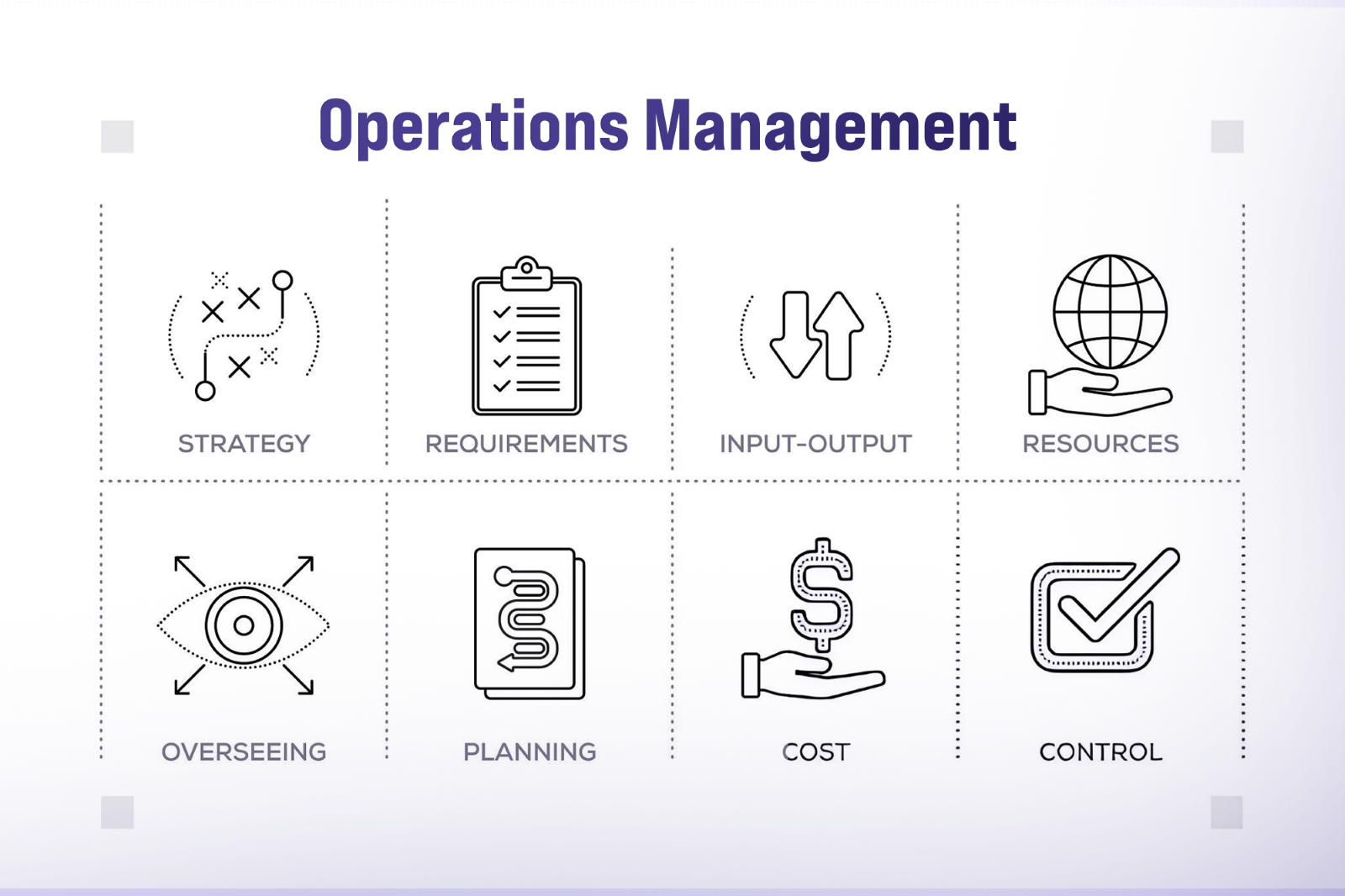
To manage the transformation of inputs (like materials, labor, capital, and information) into valuable outputs, goods, and services, operations managers focus on certain well-defined objectives set through proper research that drive both short-term efficiency and long-term sustainability.
Below are the 8 key objectives of operations management:
Achieving Efficiency and Productivity
One of the primary objectives of operations management is to boost the efficiency and productivity of production management systems. This means making the best possible use of resources like materials, equipment, labor, and time to generate the maximum output with minimal input.
Operations managers accomplish this by refining workflows, eliminating inefficiencies, minimizing delays, and confirming that each production stage contributes meaningful value. Enhanced productivity leads to lower costs and increased revenue for the business.
Delivering Superior Quality
Quality is non-negotiable in today's competitive market. Operations management focuses heavily on delivering products and services that consistently meet or exceed customer expectations.
This is done by implementing effective quality control systems, adopting quality improvement methodologies like Six Sigma or Total Quality Management (TQM), and ensuring strict adherence to industry standards. Exceptional quality not only boosts client contentment but also strengthens brand trust and market standing.
Controlling Cost and Waste Reduction
Another crucial objective is to manage and reduce production and operational costs. This is achieved by identifying areas of wastage, streamlining workflows, optimizing resource utilization, and adopting cost-effective production techniques such as Lean Manufacturing or Just-In-Time (JIT) inventory management.
The ultimate aim is to lower costs without compromising on quality, allowing the business to offer competitive prices and achieve financial sustainability.
Meeting Customer Demand Effectively
An organization's operations system must be capable of meeting customer demand accurately in terms of quantity, quality, and delivery time. Operations managers plan capacity, schedule production, and coordinate supply chains to ensure that the right products are available when customers need them.
Meeting demand reliably helps gain customer trust, retain clients, and avoid situations of stockouts or excessive inventory.
Enhancing Flexibility and Adaptability
In a dynamic market, customer preferences, technology, and business environments are constantly changing. One of the key objectives of operations management is to make production systems flexible enough to adapt quickly to these changes. Whether it’s adjusting production volumes, introducing new products, or adopting new technologies, operations managers aim to ensure that the organization stays agile and responsive.
Strengthening Supply Chain and Inventory Management
Today’s operations management plays a key role in overseeing supply chains which is the interconnected system of vendors, producers, wholesalers, and sellers. An optimized supply chain guarantees timely material sourcing, uninterrupted manufacturing, and on-time management of product distribution.
Efficient inventory management is also crucial to avoid excess stock, reduce holding costs, and prevent stockouts, maintaining a healthy balance between demand and supply.
Minimizing Risks and Disruptions
Operations managers work proactively to identify, assess, and mitigate potential risks that could disrupt production or service delivery. This includes managing supply chain uncertainties, equipment breakdowns, labor issues, or unexpected demand fluctuations. By ensuring risk management and contingency planning, operations management safeguards the organization from costly disruptions and production delays.
Promoting Coordination and Communication
Effective communication and coordination across departments, suppliers, employees, and other stakeholders is a vital objective of operations management. Seamless coordination ensures all stakeholders in production work toward shared business objectives.
Operations managers promote teamwork, cross-functional collaboration, and smooth information flow to enhance efficiency, reduce errors, and improve decision-making.
By achieving these objectives, operations management helps organizations become more profitable, customer-centric, and adaptable to the changing business world.
What is the Scope of Operations Management
The scope of operations management can be understood by the fact that it is applied to every stage of the production and delivery process. It applies not just to industrial production but is equally vital in service-based industries.
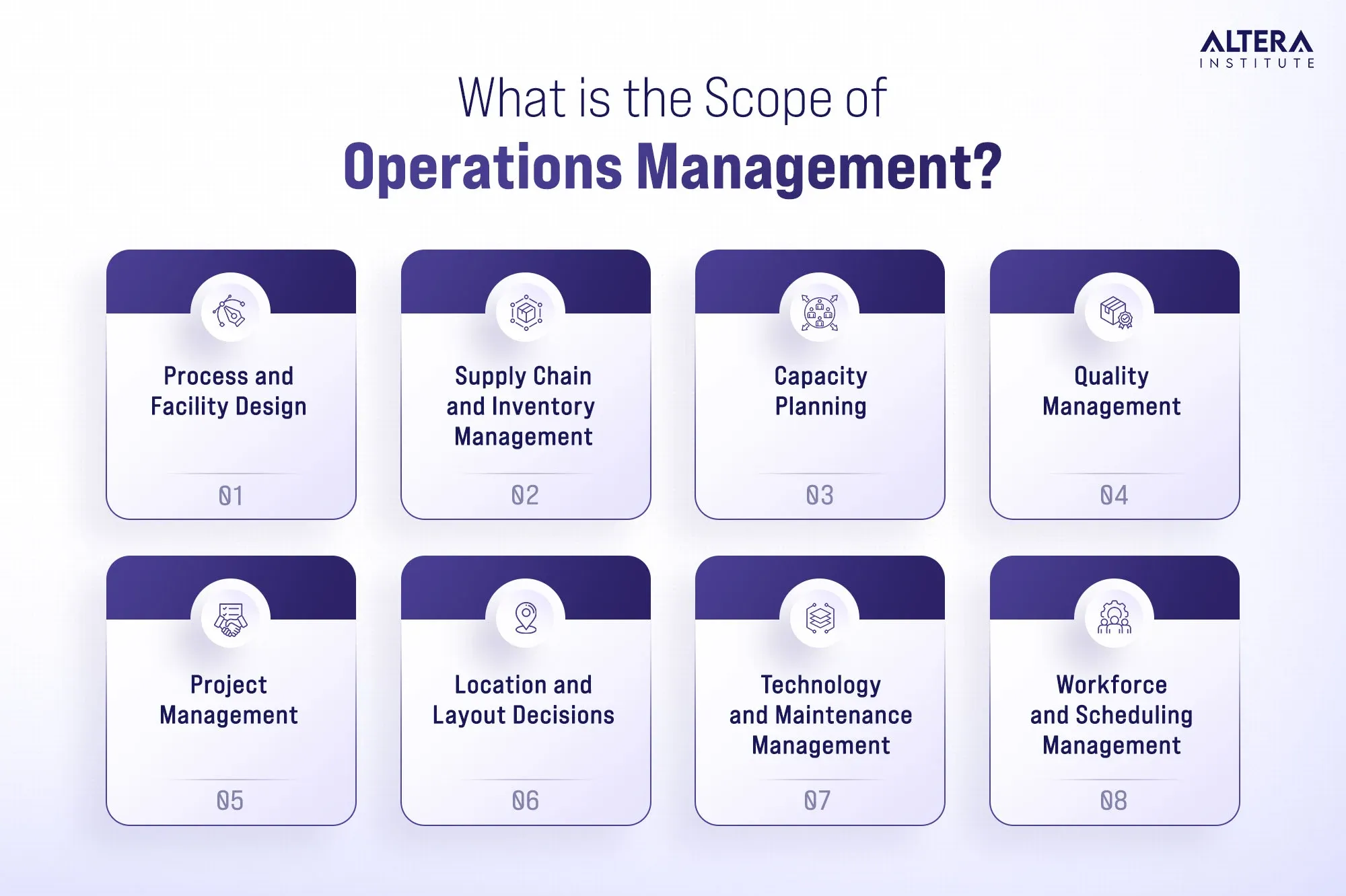
Below are the 8 major scopes of Operations Management
Process and Facility Design
The first crucial scope of operations management is designing the processes and facilities required for production. This involves planning how products or services will be produced, selecting appropriate production methods, deciding on technology, and designing workflow patterns.
Process design aims to create efficient systems by minimizing waste, reducing process time, and ensuring smooth operations. Facility design, on the other hand, deals with the optimal layout of physical spaces, equipment, and workstations to enhance productivity and reduce unnecessary movement within the facility.
Supply Chain and Inventory Management
Supply chain management governs the movement of goods, data, and funds from suppliers to consumers. Operations managers coordinate purchasing, logistics, warehousing, and distribution activities.
A crucial aspect of supply chain management is inventory control, which maintains optimal stock levels of both raw materials and final products. Efficient inventory management helps reduce carrying costs, avoid stockouts, and meet customer demand without delays or excessive inventory holding.
Capacity Planning
Capacity planning involves calculating the necessary production output to fulfill present and upcoming market needs. Operations managers assess available resources, forecast demand, and make strategic decisions about expanding, reducing, or modifying production capabilities.
The goal is to ensure that the organization neither operates below capacity (leading to underutilization) nor exceeds capacity (leading to overburdened systems), thereby maintaining a balance between cost-efficiency and responsiveness to demand fluctuations.
Quality Management
Another key responsibility is upholding product and service quality. Operations managers establish benchmarks, enforce quality checks, and drive ongoing enhancement initiatives like Total Quality Management (TQM) or Six Sigma.
Quality management ensures that the products meet customer expectations, comply with regulatory requirements, and contribute to customer satisfaction and brand reputation.
Project Management
In operations, project management plays a vital role in successfully executing specific tasks such as launching a new product, installing new equipment, or expanding facilities. Project management includes organizing, scheduling, allocating resources, and overseeing tasks within set timelines and budgets.
Operations managers frequently guide diverse teams to achieve project goals while balancing cost, quality, and deadlines.
Location and Layout Decisions
Choosing the right location for facilities such as factories, warehouses, or service centers is a critical decision in operations management. Factors like proximity to suppliers and markets, transportation costs, availability of labor, and infrastructure significantly affect the success of operations.
Once the location is finalized, operations managers focus on facility layout, which involves the arrangement of machinery, workspaces, and equipment to maximize space utilization, streamline workflows, and improve overall productivity.
Technology and Maintenance Management
Modern operations heavily rely on technology to streamline production, improve accuracy, and reduce costs. Operations managers are tasked with selecting, deploying, and overseeing technologies like automation, enterprise software, and production systems.
Moreover, maintenance management involves routine checks, servicing, and repairs of equipment to avoid failures, minimize downtime, and ensure operational continuity.
Workforce and Scheduling Management
The human element is critical in operations. Workforce planning involves recruiting, training, and managing employees to ensure that sufficient skilled personnel are available to meet production requirements.
Scheduling, on the other hand, deals with preparing work schedules that balance workload, reduce idle time, and meet deadlines. Proper workforce and scheduling management enhance employee productivity, minimize labor costs, and ensure timely delivery of products and services.
Components of Operations Management
Operations management (OM) consists of interconnected elements that collaborate to facilitate seamless production and service delivery. A company’s success hinges on how effectively these components are coordinated.
Below are the 12 key components of operations management:
Forecasting
Forecasting helps managers predict future production needs by analyzing past trends, market data, and historical records. It is vital in deciding optimal production quantities for goods or services.
Accurate forecasting prevents both overproduction, which leads to excess inventory, and underproduction, which results in missed sales opportunities. By anticipating customer demand effectively, organizations can optimize production schedules and resources.
Location Strategy
Selecting an ideal site for manufacturing plants, storage hubs, or service centers is a pivotal choice that greatly influences operational success. Factors like availability of raw materials, access to skilled labor, transportation costs, proximity to customers, and infrastructure are considered. A well-planned location strategy helps reduce operational costs, improve delivery speed, and support the long-term objectives of the organization.
Maintenance Management
This component focuses on the upkeep and servicing of machinery, equipment, and production systems. Regular maintenance minimizes the risk of sudden equipment breakdowns, enhances workplace safety, and ensures that machines operate at peak efficiency. Proper maintenance extends the lifespan of assets and helps maintain uninterrupted production, ultimately contributing to cost savings and productivity.
Purchasing
Purchasing, or procurement entails securing the necessary inputs, parts, and services required for manufacturing. Organizations may follow centralized purchasing (managed by a central department) or decentralized purchasing (managed individually by branches or departments).
An efficient purchasing system ensures the timely availability of materials, helps negotiate better deals with suppliers, and reduces material-related production delays.
Scheduling
Scheduling refers to assigning tasks, jobs, or production runs to the appropriate equipment or workforce. A well-prepared schedule ensures that production deadlines are met without overburdening resources. Proper scheduling reduces idle time, speeds up production cycles, and helps meet delivery commitments. This leads to better utilization of machines, labor, and other resources.
Total Quality Management (TQM)
TQM is a continuous improvement approach focused on customer satisfaction by involving all employees in improving processes. Rather than just checking the quality of finished products, TQM emphasizes improving production methods and systems to reduce defects and enhance efficiency. The goal is to reliably provide outputs that satisfy or outperform customer needs.
Materials Requirement Planning (MRP)
MRP is a structured method to guarantee materials are available in precise amounts and timelines to support manufacturing plans. It involves analyzing existing inventory, determining additional material requirements, and planning procurement or production. MRP helps organizations avoid production delays caused by material shortages and prevents unnecessary excess inventory.
Quality Assurance
Quality is the cornerstone of operations management. Quality control verifies that outputs adhere to predefined benchmarks. By maintaining high-quality standards, organizations build trust and long-term relationships with customers. Effective quality control processes reduce errors, minimize waste, and improve customer satisfaction.
Just-In-Time (JIT) Production
JIT is a strategy where materials, components, and products are manufactured or acquired exactly when they are needed, rather than being stored in large quantities. This approach minimizes inventory costs, reduces work-in-progress (WIP) inventory, and improves the flow of materials throughout the production process. JIT strives to maximize efficiency, cut waste, and fulfill customer orders promptly.
Process and Performance Analysis
This component concentrates on assessing the effectiveness of production systems and procedures. Managers compare planned production targets with actual performance in terms of capacity utilization, efficiency, and output levels. By examining gaps and inefficiencies, companies can pinpoint improvement opportunities and implement solutions to boost performance.
Facility Layout Planning
Facility layout involves designing the physical arrangement of equipment, workspaces, and storage areas to optimize workflow. A well-planned layout reduces unnecessary movement of materials, shortens production cycles, and promotes efficient use of space and labor. An efficient facility design reduces waste, shortens production cycles, and elevates output.
Inventory Management
Inventory management deals with monitoring and controlling raw materials, semi-finished goods, and finished products. Strategic inventory management prevents both surpluses and shortages of stock. Maintaining optimal inventory levels helps organizations meet customer demand promptly while minimizing holding and storage costs.
What Are the Roles of an Operations Manager?
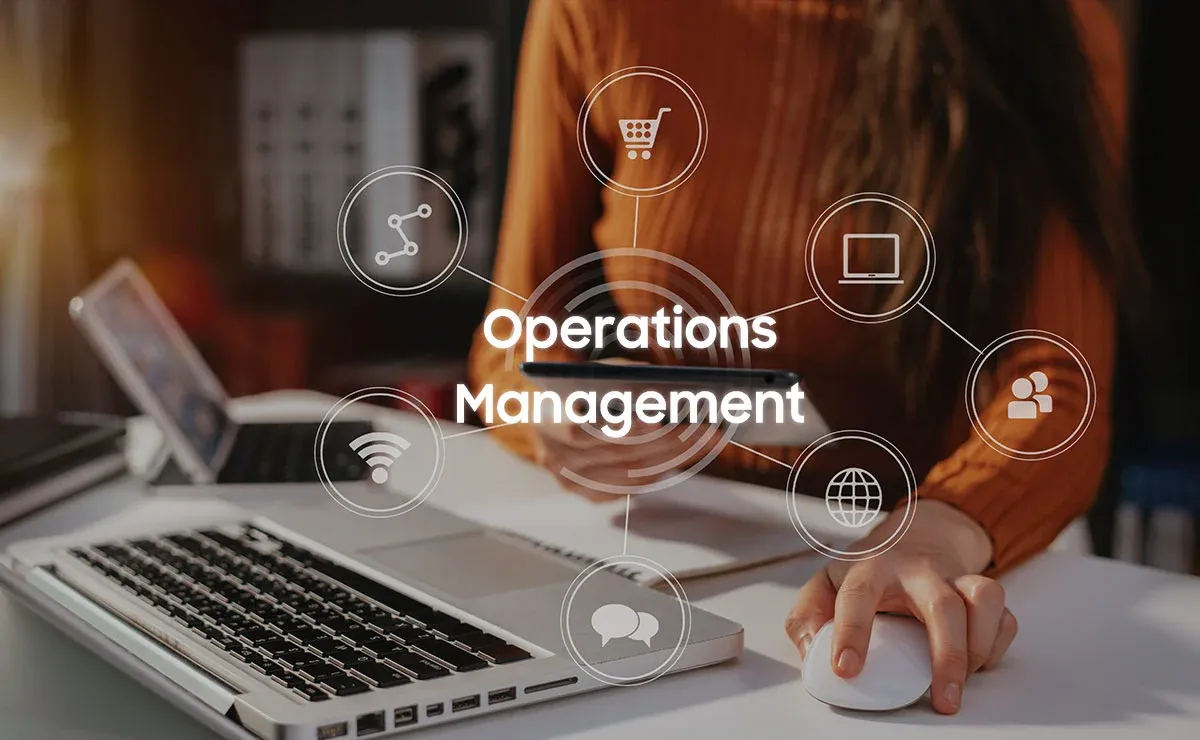
An operations manager is pivotal in supervising and refining production and service marketing processes. Their main duty is ensuring daily operations align with business objectives while running seamlessly. The key roles of an operations manager include:
- Enhancing existing systems, processes, and best practices to boost productivity and operational efficiency.
- Monitoring and managing the production or service processes to ensure smooth operations and desired output quality.
- Handling budgets to ensure optimal use of financial resources while maintaining cost-effectiveness.
- Leading the operations team by assigning tasks, setting deadlines, monitoring employee performance, and fostering a positive work environment.
- Managing material sourcing, stock planning, and warehousing to maintain smooth supply chain activities.
- Developing and nurturing partnerships with suppliers to fulfill organizational requirements efficiently.
- Performing risk evaluations and deploying mitigation tactics to lessen operational vulnerabilities.
- Reviewing financial and operational metrics to uncover profit-boosting opportunities and cost-saving measures.
- Guaranteeing product quality through routine inspections and monitoring performance metrics.
In summary, an operations manager is responsible for optimizing resources, improving processes, managing people, and maintaining quality to achieve operational excellence.
FAQs
Q1. What are the 7 main functions of operations management?
Ans: The seven main functions of operations management are as follows:
- Process Design – Designing efficient production processes.
- Capacity Planning – Matching production capacity with demand.
- Inventory Management – Controlling raw materials, WIP, and finished goods.
- Supply Chain Management – Coordinating the movement of resources and information.
- Quality Management – Maintaining adherence to quality in products and services.
- Scheduling – Planning production timelines effectively.
- Maintenance Management – Ensuring equipment runs smoothly with minimal downtime.
Q2. What is the scope of operations of a company?
Ans: The scope of operations of a company covers all activities involved in producing and delivering goods or services. It includes:
- Product and process design
- Production management
- Supply chain and logistics
- Inventory and quality control
- Maintenance
- Continuous improvement initiatives.
Q3. What career scope does an MBA in operations management offer?
Ans: An MBA in operations management prepares professionals for careers in production, supply chain, logistics, quality management, and project management. It opens doors in sectors like manufacturing, retail marketing , healthcare, IT, and consulting, with positions such as operations lead, logistics coordinator, and project supervisor.
Summing Up
Operations management is the backbone of any successful organization, playing a vital role in transforming inputs into valuable outputs while ensuring efficiency, quality, and customer satisfaction. Its scope is vast, covering everything from process design and capacity planning to supply chain management and quality control.
In today’s fast-paced, competitive market, robust operations management is key to reaching business targets, sustaining profits, and delivering exceptional customer value.
Whether you are a student, a manager, or an aspiring operations professional, understanding the principles, functions, and scope of operations management is key to driving sustainable success in any industry.