What is the Scope of Material Management?
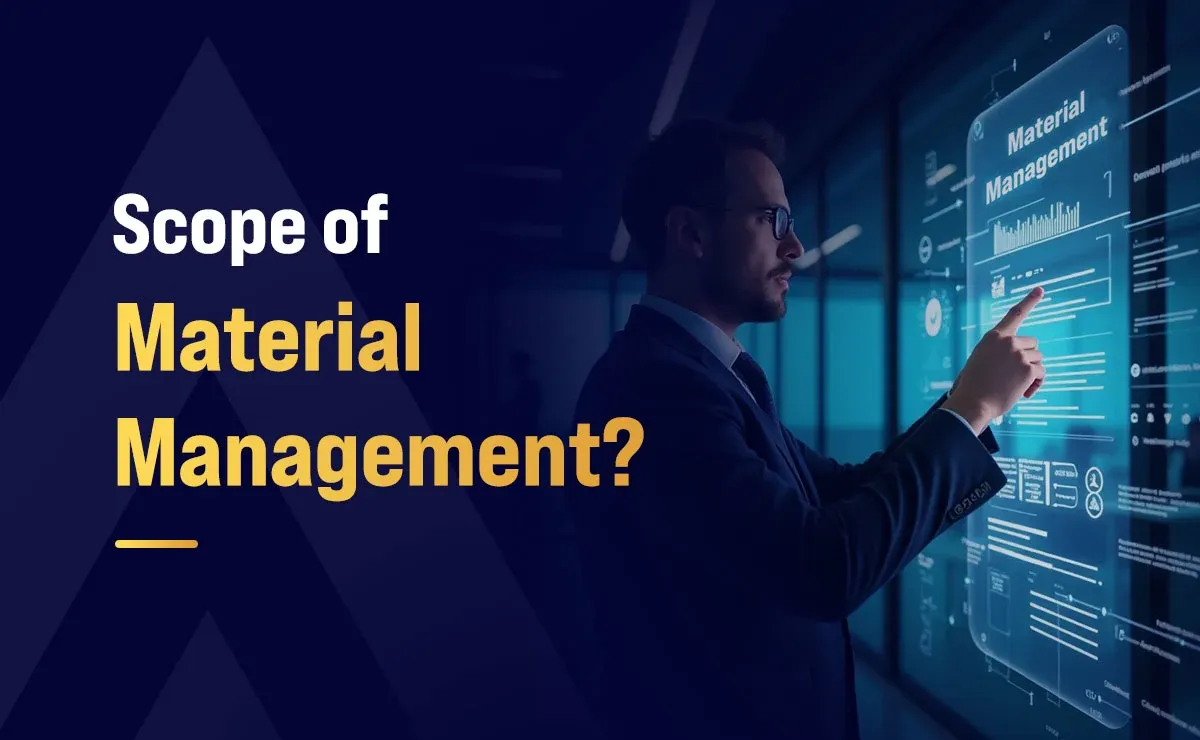
Material management is a vital organizational function, particularly in production, logistics, and supply chain operations, ensuring seamless workflow and resource optimization. It ensures the smooth flow of materials from sourcing to final utilization, directly impacting efficiency, cost-effectiveness, and productivity.
The scope of material management involves planning, organizing, and controlling materials from procurement to final use, optimizing costs, ensuring timely availability, minimizing waste, and enhancing overall supply chain efficiency. Moreover, it is also evolving to include innovative strategies such as automation, artificial intelligence (AI), and just-in-time (JIT) delivery.
This article explores the scope of material management, its key functions, and the principles that guide its efficient execution.
What is Material Management?
Material management refers to the process of sourcing, purchasing, storing, controlling, and distributing materials in a way that aligns with business objectives. It guarantees that necessary materials are accessible when needed, in precise amounts, and at optimal costs to prevent production halts, overstocking, and operational inefficiencies.
The core aim of material management is to balance supply and demand while optimizing costs and maintaining product quality. This function is deeply interconnected with supply chain management, logistics, inventory management, and strategic procurement processes.
Scope of Material Management
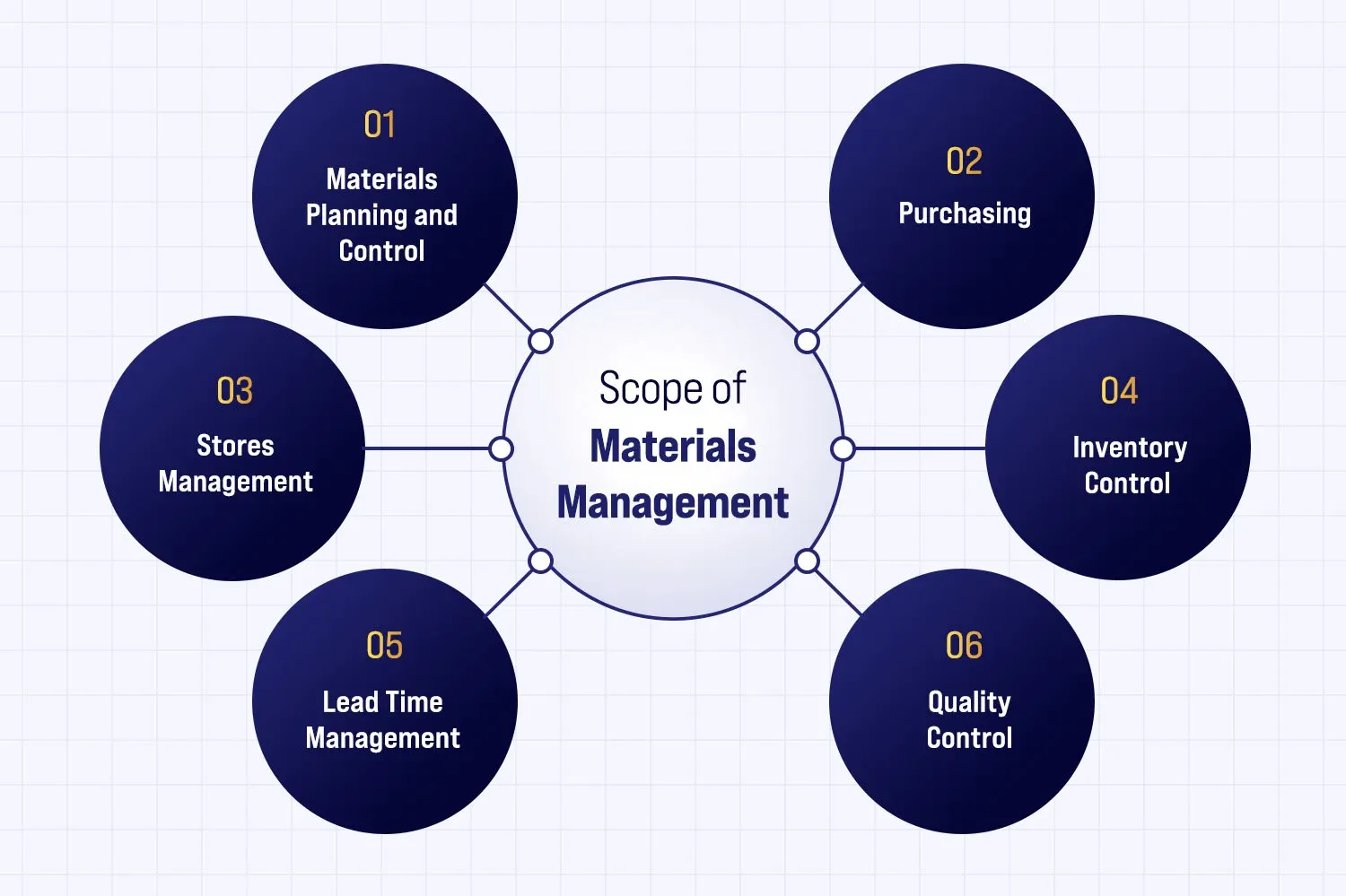
The scope of material management encompasses various aspects of handling materials throughout their lifecycle. From planning and procurement to storage and inventory control, every stage plays a vital role in ensuring operational efficiency. Below are the key areas covered under material management:
Materials Planning and Control
Materials planning and control form the foundation of effective materials management. It involves determining material requirements based on projected demand and production plans. Its primary objective is maintaining the perfect balance of materials, which is neither too little to cause shortages nor too much to incur unnecessary storage costs.
Key Tasks
- Demand Forecasting: Estimating future material requirements using production timelines, past data analysis, and industry trends.
- Budgeting and Cost Control: Crafting a financial plan for materials and distributing funds wisely to prevent budget overruns.
- Order Scheduling: Planning procurement timelines to ensure materials are available in sync with production management cycles.
- Performance Monitoring: Tracking stock usage and adjusting plans based on actual consumption and market fluctuations.
By aligning material availability with production timelines, this function helps in reducing both stockouts and excess inventory.
Purchasing
Purchasing involves sourcing materials economically, promptly, and without compromising quality standards. It covers:
- Vendor Selection and Evaluation: Identifying reliable suppliers based on price, quality standards, and delivery track record.
- Negotiation and Contracting: Finalizing procurement terms to optimize cost and delivery schedules.
- Purchase Order Management: Overseeing order placement, approvals, and timely follow-ups.
An efficient purchasing process ensures a stable flow of materials into the organization, promoting consistent production and minimizing procurement-related risks.
Stores Management
Efficient stores management ensures proper handling, storage, and security of materials. Key activities include:
- Warehouse Layout Optimization: Organizing storage areas for easy access and efficient movement.
- Stock Record Maintenance: Keeping accurate records of materials to track usage and availability.
- Quality Preservation: Ensuring materials are stored under suitable conditions to prevent damage.
Effective stores management reduces waste, prevents losses, and supports timely production through well-maintained inventory systems.
Inventory Control
Inventory control ensures stock levels align with production demands while reducing storage expenses and space constraints, striking a balance between availability and cost efficiency.
Key Tasks
- ABC Analysis: Classifying inventory based on usage value and criticality to prioritize management efforts.
- Just-in-Time (JIT): Acquiring materials precisely as required, cutting down on storage needs and minimizing waste.
- Economic Order Quantity (EOQ): Determining the most cost-effective purchase quantity to optimize ordering and storage expenses.
- Reorder Point Planning: Setting automatic restocking thresholds based on consumption patterns and delivery timelines.
The ultimate goal is to maintain production flow without overburdening storage facilities or increasing capital investment in excess stock.
Lead Time Management
Lead time management focuses on optimizing the gap between order initiation and material arrival, ensuring production flows smoothly without procurement-related interruptions.
Key Tasks
- Lead Time Analysis: Evaluating each stage of the procurement and delivery cycle to identify bottlenecks.
- Supply Chain Coordination: Building tight collaborations with vendors and transportation networks to eliminate bottlenecks and keep operations management smooth and running on schedule.
- Reorder Timing: Factoring in lead time while determining reorder points to maintain consistent material flow.
Quality Control
Quality control is essential to maintaining the integrity of materials and ensuring that only compliant and high-quality inputs are used in production.
Key Tasks
- Cross-Functional Coordination: Coordinating with procurement and inventory teams ensures that materials are sourced and stocked in time to meet production requirements.
- Synchronizing Supply with Production: Aligning material supply with production timelines helps avoid interruptions, ensuring a smooth and continuous manufacturing process.
- Dynamic Monitoring and Adjustment: Monitoring production progress and adjusting material planning allows for flexibility in handling unexpected changes in demand or production pace.
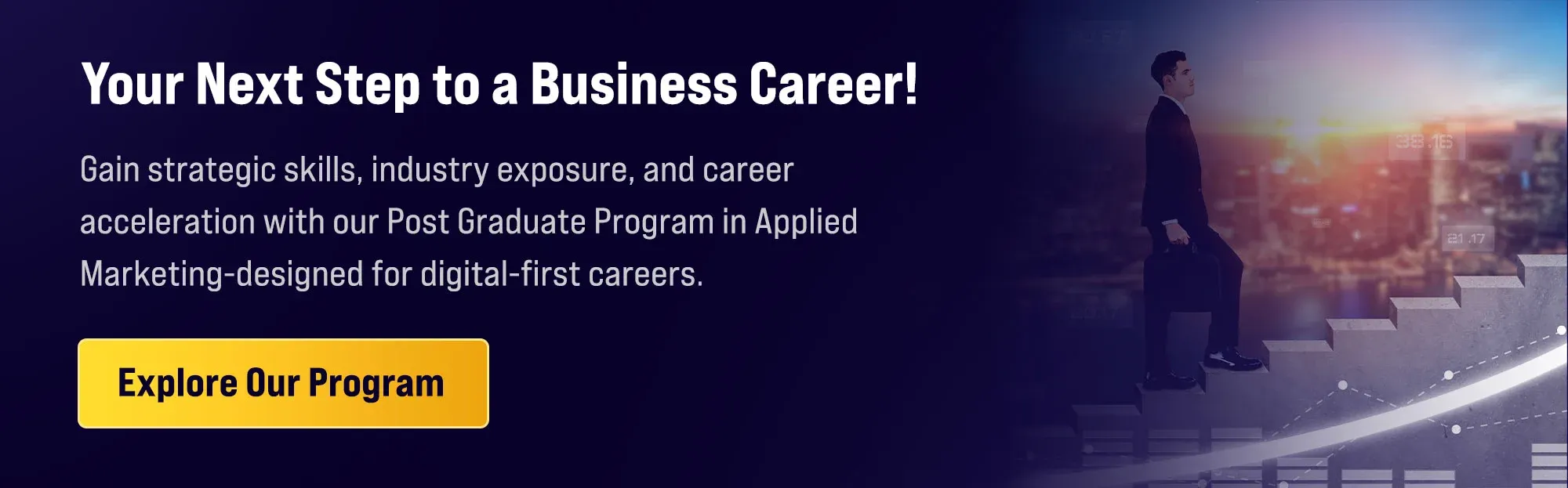
Functions of Material Management
Material management is an essential backbone of operations, facilitating uninterrupted material flow across all organizational stages. Other than material planning, purchasing, stores management, and inventory control, here are more key functions that define a robust materials management system:

Standardization
Standardization aims to reduce the variety of materials, parts, and processes used by establishing uniform specifications and quality benchmarks to ensure consistency, simplify operations, and reduce costs.
Key Tasks:
- Develop and implement specifications for commonly used materials and parts.
- Ensure that standardized materials are used across multiple products and processes.
- Facilitate compatibility and interchangeability of components by adhering to set standards.
- Work with suppliers to procure materials that meet the established criteria.
Simplification
Simplification is the deliberate reduction of product variety, materials, and processes to achieve efficiency, reduce redundancy, and simplify inventory and purchasing activities.
Key Tasks
- Evaluate the range of products and components to identify overlaps or redundancies.
- Eliminate low-demand or obsolete items to simplify inventory management.
- Standardize parts and processes to reduce variation and complexity.
- Consolidate the supplier base and material categories to improve control and efficiency.
Specifications
Specifications are detailed, precise statements outlining the technical and functional requirements of a product, material, process, or service. They serve as formalized guidelines that define the standards a material or product must meet to fulfill its intended purpose.
Key Tasks
- To clearly communicate customer or engineering requirements.
- To ensure consistency and accuracy in procurement and production.
- To provide measurable criteria for quality inspection and acceptance.
- To minimize ambiguity and prevent quality deviations.
Value Analysis
Value analysis is a methodical evaluation of each component in a product or material to maximize functionality while minimizing expenses and maintaining quality.
Key Tasks
- Break down products into functional components to understand their role and cost contribution.
- Identify high-cost areas where alternative materials or methods can be used.
- Explore design modifications that could reduce production costs.
- Collaborate across teams—engineering, procurement, and finance—to implement cost-effective solutions.
Ergonomics
Ergonomics in material management involves designing systems, tools, and workflows that are safe, efficient, and human-friendly, especially during material handling and storage operations.
Key Tasks
- Design workplace layouts and storage systems that reduce worker fatigue and increase efficiency.
- Choose user-friendly equipment and controls that enhance efficiency and minimize physical stress.
- Implement safety measures that prevent accidents during material handling.
- Continuously review and improve working conditions for optimal productivity.
Just-in-Time (JIT)
JIT revolutionizes inventory control by synchronizing material deliveries with exact production demands, eliminating wasteful stockpiling practices.
Key Tasks
- Foster reliable partnerships with suppliers to guarantee punctual material deliveries.
- Reduce reliance on safety stock by improving demand forecasting accuracy.
- Align production schedules closely with material delivery schedules.
- Track supplier reliability and performance to maintain steady and dependable supply chains.
When executed effectively, material management reduces costs and enhances product quality, employee productivity, and customer satisfaction.
FAQs
Q1. What is the scope of management?
Ans: The scope of management encompasses all activities related to planning, organizing, directing, and controlling resources—human, financial, physical, and informational—to achieve organizational objectives efficiently and effectively. It covers various functional areas such as production, marketing, finance, human resources, and operations, ensuring coordination and optimal utilization of resources across all departments.
Q2. What is the scope of material control?
Ans: The scope of material control involves regulating the flow and usage of materials within an organization to ensure adequate supply for production without incurring excessive inventory costs. It includes forecasting material requirements, monitoring stock levels, maintaining accurate records, implementing reorder policies, and minimizing losses due to wastage, theft, or obsolescence. Effective material control ensures smooth production processes and cost efficiency.
Q3. What is the scope of material handling?
Ans: The domain of material handling encompasses transporting, safeguarding, storing, and regulating materials across production, warehousing, distribution, usage, and disposal phases. It involves selecting appropriate handling equipment, designing efficient layouts, ensuring worker safety, and optimizing the flow of materials to reduce handling costs and improve productivity.
Q4. What are the 3S of material management?
Ans: The 3S of material management are Sort, Set in Order, and Shine. These are the first steps in the 5S methodology, aimed at improving workplace efficiency:
- Sort: Remove unnecessary items to keep only what’s needed.
- Set in Order: Organize and label items so they’re easy to find and return.
- Shine: Clean the workspace regularly to maintain order and spot issues early.
These practices reduce waste, improve safety, and enhance productivity.
Summing Up
Material management is a foundational pillar of operational success in any production or supply chain-driven organization. By efficiently managing the flow of materials—from planning and procurement to storage, handling, and usage—organizations can achieve cost savings, streamline operations, and enhance product quality.
In essence, effective material management not only supports the smooth execution of day-to-day operations but also drives long-term business value by optimizing resources, reducing waste, and enhancing customer satisfaction.